Electropolishing is a process known for achieving exceptionally smooth and clean surfaces in metal finishing. From medical device manufacturing to aerospace engineering, this versatile metal finishing technique has become indispensable across various industries. In this article, we explore the process of electropolishing, its benefits, and the wide range of applications that rely on this sophisticated surface treatment method.
Sections
ToggleWhat is Electropolishing?
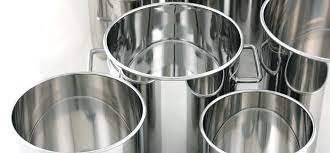
Electropolishing, also known as electrochemical polishing, is an electrochemical process that removes a thin layer of metal from the surface of a metal part, resulting in a smooth, bright, and highly polished finish.
In contrast to mechanical polishing methods that rely on abrasives to smooth out surface irregularities, electropolishing is much more efficient. It uses a combination of electricity and a specially formulated electrolyte solution to dissolve the outermost layer of metal atoms selectively. This process offers several other advantages over mechanical polishing, not only simplicity. Mechanical methods leave residual stresses and potentially embed abrasive particles in the metal surface. It produces a subpar finish, while electropolishing produces a stress-free surface with no risk of contamination. Additionally, electropolishing is a chemical process, so it can reach areas that are difficult or impossible to access with traditional polishing tools.
How Does Electropolishing Work?

Electropolishing uses the basic principles of the electrochemical reaction. To understand how electropolishing works, you must know the key elements of the process. Electroplating has three main components:
- Electrolytes are chemical solutions that accelerate the dissolution of metal ions.
- Anode-cathode: The metal piece usually acts as an anode, releasing metal ions, and another metal is used that acts as the negative electrode.
- Electric current is the third element providing the force for electrochemical reactions.
The electropolishing process has three main steps:
- First, the metal piece is immersed in an electrolyte bath and connected to the positive pole acting as anode in the electrical circuit.
- A cathode (negative electrode) is placed in the electrolyte, typically made of a material that won’t dissolve during the process.
- Electric current is passed through the circuit, dissolving the metal ions from the metal’s surface and dividing them into the electrolyte solution. Hydrogen gas is typically produced at the cathode.
How Much Material is Removed by Electropolishing?
The amount of material removed during the electropolishing process typically ranges from 0.0003 to 0.0005 inches (5 to 10 micrometers) per surface. However, this is a general assumption, and the actual number can vary depending on several factors:
- Duration of the electropolishing
- Current density applied to the circuit
- Composition of the electrolyte
- Type of metal being polished
- Initial surface condition of the workpiece
Electropolishing removes material preferentially from peaks and protrusions, effectively levelling the surface. It implies that the amount of material from the metal surface can vary across the surface of a single part.
Benefits of Electropolishing

Electrolytic polishing offers a wide range of benefits, which makes it a reliable option for many industries and applications:
- Enhanced corrosion resistance: Electropolishing is widely used across industries to improve corrosion resistance. For example, electropolishing stainless steel removes the outermost metal layer, exposing a chromium-rich surface. It significantly reduces the risks of corrosion.
- Improved surface finish and hygiene: The electropolished surface is exceptionally smooth. With no groves to accumulate dirt and allow easy cleaning, it reduces the potential for bacterial adhesion. This is particularly crucial in the medical and food processing industries.
- Reduction of surface stresses: Unlike mechanical polishing methods, electropolishing uses no abrasive to smoothen the surface. Therefore, it doesn’t introduce new stresses into the material. On the contrary, the process can help relieve existing surface stresses, improving fatigue resistance.
- Aesthetic improvements: Electropolishing produces a bright, reflective surface that is visually appealing. It also removes small burrs and sharp edges, improving not only aesthetics but also functionality and safety.
Common Applications for Electropolishing
You can find several industries using electropolishing because it can produce ultra-clean, smooth, and corrosion-resistant surfaces. Among key sectors that rely on electropolishing services are:
- Medical and Pharmaceutical: The process improves the surface of surgical instruments, implants, and drug manufacturing equipment.
- Aerospace: Electropolishing improves the surface quality of turbine blades, hydraulic components, and fasteners.
- Food and Beverage Processing: Electropolishing improves the quality and hygiene of tanks, pipes, valves, and mixing equipment.
- Semiconductor and Electronics: As an electrochemical polishing, it is also beneficial for improving the surface quality of vacuum chambers, wafer handling equipment, and precision components.
- Automotive: Some electropolished items include fuel injection systems, exhaust components, and decorative trim.
Electropolishing Stainless Steel

Across industries, electropolishing stainless steel is a common practice. The reason is that stainless steel components are widely used for corrosion resistance and cleanliness; using this surface treatment technique further improves the qualities of the metal.
Benefits of Electropolishing Stainless Steel
There are several benefits of electropolishing stainless steel:
- Enhanced corrosion resistance: Through electropolishing, the iron ions are selectively removed from the surface of stainless steel, leaving only a chromium-rich layer. This significantly improves the corrosion resistance of stainless steel.
- Improved aesthetics: While the stainless steel surface is relatively smooth, the moulding or turning process introduces irregularities on the surface of metal parts. By electropolishing, the surface can be made bright and reflective, which is both attractive and functional.
- Increased durability: The risk of pitting and crevice corrosion is significantly reduced by smoothening the surface by electropolishing stainless steel. It could extend the lifespan of stainless steel components.
- Easier cleaning and maintenance: The ultra-smooth surface of electropolished stainless steel is naturally resistant to the adhesion of contaminants. It makes the surface easier to clean and is ideal for hygienic applications.
Electropolishing of Stainless Steel After Welding
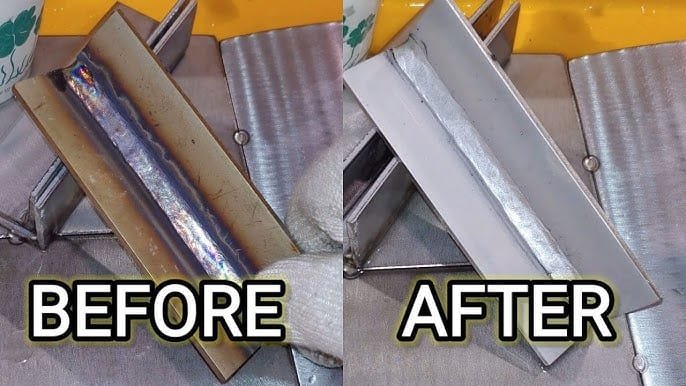
The natural smoothness and corrosion resistance properties are hampered when parts are manufactured using welding. Welding stainless steel can present several challenges, including discoloration, roughness, and potential changes in corrosion resistance in the heat-affected zone.
With electropolishing stainless steel, these issues can be addressed effectively:
- Removal of heat tint: Electropolishing can effectively remove the discoloration caused by welding. It can quickly restore the uniform appearance of the entire stainless steel surface.
- Smoothing of weld beads: Electrolytic polishing is a better alternative than mechanical methods for blending the weld area with the surrounding metal, reducing surface irregularities.
- Restoration of corrosion resistance: By removing the heat-affected layer and weld beads, electropolishing exposes fresh, chromium-rich stainless steel, restoring corrosion resistance.
Electropolishing Benefits for Metal Alloys
Apart from stainless steel, electropolishing can benefit a variety of other metals and alloys:
- Aluminum: Electropolishing aluminum can produce a bright, reflective finish and improve corrosion resistance.
- Titanium: Electropolishing is widely used in aerospace and medical applications to improve the surface quality of titanium.
- Copper and copper alloys: Electropolishing also works with copper and copper alloys and enhances the conductivity of copper components.
- Nickel and nickel alloys: You can also use electropolishing to improve nickel’s corrosion resistance and surface finish.
You must carefully consider the choice of electrolyte and process parameters when electropolishing a specific type of metal. An experienced electropolisher can tailor the process to achieve optimal results for each material.
Process Steps: How to Electropolish Stainless Steel
The process of electropolishing stainless steel is simple, typically involving three basic steps:
- Surface Preparation: For effective and quality electropolishing, the surface of stainless steel components should be cleaned to remove oils, greases, and other contaminants. It is essential to degrease the surface using alkaline or solvent-based cleaners.
- Electropolishing: The metal is immersed in the electrolyte bath after surface preparation. The current is applied for a specified time, and the electrolyte and workpiece are continuously agitated to ensure uniform polishing.
- Post-Dip: Finally, the metal piece is rinsed in deionized water to remove residual electrolyte. Sometimes, it is followed by passivation treatment to enhance corrosion resistance further.
Electropolishing as a Secondary Finishing Process
Usually, electropolishing is used as a secondary finishing process after the manufacturing of a component is complete. Some techniques using electropolishing as a secondary finishing include:
- Post-machining: Electropolishing removes tool marks and improves surface finish after CNC machining or other cutting processes.
- Post-welding: As mentioned earlier, electropolishing can help address issues such as weld beads and heat tint.
- Post-forming: For parts that have been formed or bent, electropolishing can help relieve surface stresses and improve corrosion resistance.
- Final finishing: In manufacturing, electropolishing is often the last step for surface finish, cleanliness, and corrosion resistance.
By integrating electropolishing into the manufacturing process, manufacturers can enhance the surface properties of their products post-production. This creates premium-quality metal components that meet stringent industry standards.
Best Practices for Electrochemical Polishing
You should consider the best practices for electropolishing any metal surface for best results. It includes:
- Equipment maintenance: Regularly clean and maintain electropolishing equipment to ensure that the process produces consistent results.
- Proper selection of electrolytes: Wrong electrolytes will not dissolve target metal ions. For effectiveness, the selected electrolyte must be compatible with the polished metal.
- Monitoring process parameters: Also, the electropolishing process depends on parameters such as temperature, voltage, and current density. These parameters must be closely monitored and kept consistent throughout the process.
Conclusion
Electropolishing offers unparalleled benefits in terms of surface finish, corrosion resistance, and cleanliness. Whether you are considering a metal finishing process for medical implants or want to improve the corrosion resistance of aerospace components, electropolishing is an ideal process offering a versatile solution that can be tailored to meet a wide range of needs.
FAQs
- Is electropolishing better than passivation?
Electropolishing is generally more effective than passivation as it removes a thin layer of metal, improving corrosion resistance, surface smoothness, and appearance. Passivation only removes free iron and contaminants, providing less surface refinement. - Does electropolishing remove scratches?
Electropolishing can remove fine scratches and surface imperfections by dissolving a thin layer of metal. However, deeper scratches may require mechanical polishing before electropolishing for a completely smooth finish.