In the manufacturing section, whether cannabis or pharmaceuticals, solvents play a crucial role. The challenge is the financial and environmental costs associated with these volatile compounds. That’s why solvent recovery is essential across industries. This approach offers businesses a way to reclaim and reuse solvents rather than disposing of them after a single use.
With the implementation of efficient solvent recovery technologies, businesses can manage their raw material costs, stricter environmental regulations, and growing sustainability commitments. Here, we explore the process of solvent recovery in detail.
Sections
ToggleWhat is Solvent Recovery?

Solvent recovery is collecting, purifying, and reusing solvents after initial application in manufacturing or processing operations. It is part of a closed-loop system that ensures minimal wastage and that solvents can be repeatedly utilized in production cycles.
Why Do Businesses Opt for Solvent Recovery?
- Cost Efficiency: Solvents, especially hydrocarbons such as butane and propane, can be expensive. The solvent recovery process can significantly reduce costs, resulting in 60-80% savings on solvent expenses.
- Sustainability: Recovery of solvents decreases dumping hazardous waste generation and reduces the carbon footprint.
- Regulatory Compliance: Implementing solvent recovery systems helps businesses meet increasingly stringent environmental regulations such as VOC emissions and hazardous waste disposal requirements.
How Does Solvent Recovery Work?

The solvent recovery process involves separating solvents from contaminants and other undesired substances. The process can be physical or chemical depending on the differences in properties of solvent and contaminants, such as boiling point, molecular size, or chemical affinity. The recovered solvent can then be returned to the production process.
Key Methods of Solvent Recovery
1. Distillation (Simple vs. Fractional)
The most widely used technique of solvent recovery is distillation. There are two variations:
- Simple Distillation
Simple distillation relies on differences in boiling points to separate solvents from contaminants. The process heats the solvent mixture in a distillation chamber to vaporize the solvent, which is then condensed into liquid form in a separate collection vessel. This method is used when there is a significant difference (at least 25°C) between the boiling points of the solvent and contaminants. - Fractional Distillation
A more sophisticated process, fractional distillation, uses a fractionating column to achieve better separation. This solvent distillation raises vapors through multiple vaporization-condensation cycles, resulting in a more precise separation of compounds with similar boiling points.
2. Filtration & Adsorption
Filtration and adsorption techniques capture solvent molecules using specialized materials that physically trap contaminants or chemically attract the solvent. Usually, activated carbon, silica gel, and molecular sieves are used as adsorbents to capture solvent molecules selectively. This method is beneficial for removing particulates and dissolved impurities that might not be effectively separated through distillation alone.
3. Membrane Separation
A more advanced recovery method, membrane separation, uses semi-permeable barriers that selectively allow solvents to pass through while blocking contaminants. Pervaporation, nanofiltration, and reverse osmosis systems are the most common membrane separation techniques. This solvent recovery process is energy efficient and can operate at lower temperatures than traditional solvent distillation methods.
What Solvents Can Be Recovered?
Any industrial solvent can be effectively reclaimed through an appropriate solvent recovery method. Typically, the recovery rates range from 75% to 95% in the cannabis industry, depending on the specific solvent and process conditions.
Commonly Recovered Solvents:
- Acetone: Is the most widely used solvent in laboratories and electronics manufacturing, and acetone can be efficiently recovered as a cleaning agent.
- Ethanol & Methanol: These solvents are commonly recovered in pharmaceutical manufacturing, cannabis solvent recovery, and chemical synthesis.
- Toluene & Xylene: Essential in paint manufacturing, adhesives, and printing industries, these solvents have also been recovered.
- Hexane & Isopropyl Alcohol: Common solvents for extraction processes, cleaning applications, and reaction media are recovered through closed-loop systems.
Factors Influencing Recoverability:
- Boiling point: Solvents with distinct boiling points from contaminants can be easily recovered through simple distillation.
- Purity requirements: Depending on the purity required, some applications may limit the number of recovery cycles possible.
- Contamination levels: Solvents may need multiple purification steps or specialized treatment if they are heavily contaminated.
Recover. Reuse. Reduce.
Fractional vs. Simple Distillation: Which One is Right for You?
Feature | Simple Distillation | Fractional Distillation |
Best for | Single solvents with non-volatile contaminants, Solvents with widely different boiling points (>25°C difference) | Multiple solvents or components with similar boiling points (<25°C difference) |
Purity Level | Produces 90-95% purity | Achieves high purity (99%+) |
Process | Simple single vaporization-condensation cycle | Multiple vaporization-condensation cycles |
Applications | Recovery of basic cleaning solvents, single-solvent recovery systems | Ideal for recovery solvents in pharmaceutical manufacturing, cannabis processing, and multi-solvent mixtures |
Equipment Complexity | Simple setup with basic heating, condensation, and collection components | More complex with fractionating column, reflux management, and potentially multiple collection points |
Cost | Low investment and operating costs | Higher initial investment and potentially higher energy consumption |
The Efficiency & Cost Benefits of Solvent Recovery
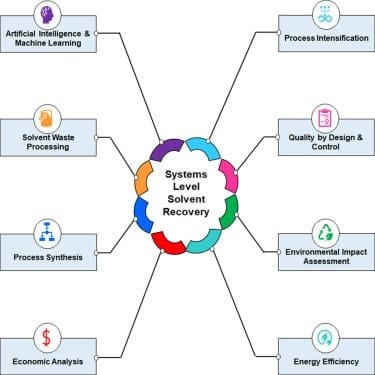
Key Benefits:
- Financial Savings: With solvent recovery, companies easily reduce purchasing and disposal costs.
- Waste Minimization: The solvent recovery process not only reduces hazardous waste volumes but also decreases disposal costs and environmental liability.
- Environmental Impact: Recovery of solvents prevents chemicals from entering the environment.
- Regulatory Compliance: Solvent recovery helps businesses stay ahead of tightening regulations.
- Improved ROI: Apart from direct solvent costs, businesses benefit from reduced insurance premiums, improved safety profiles, and enhanced sustainability credentials.
How Much Solvent Can Be Recovered?
It depends on several factors, including the efficiency of the recovery process.
Factors Affecting Recovery Rates:
- Purity Level: If higher purity is needed, the overall recovery percentages may be lower as more solvent is sacrificed during purification.
- Contamination: The nature and concentration of contaminants significantly impact recovery efficiency. It also decides the number of possible recovery cycles.
- Technology Used: More advanced solvent recovery systems generally achieve higher recovery rates than basic equipment.
Typical Recovery Percentages:
- Ethanol (Cannabis Extraction) – 85-95%
- Acetone (Pharmaceuticals, Coatings) – 80-90%
- Toluene (Paints, Adhesives) – 75-85%
Conclusion
Solvent recovery is a cost-saving opportunity for businesses and a solution for environmental sustainability. In some industries, particularly in cannabis processing, the increasing regulatory pressure means implementing effective solvent recovery process systems is no longer just an option but a necessity.